Darmstadt electron accelerator
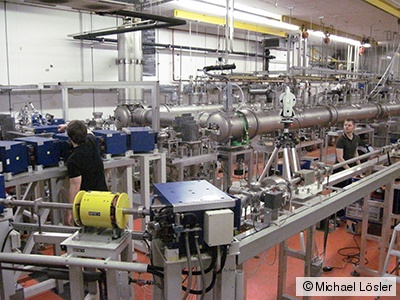
The Superconducting Darmstadt Electron Linear Accelerator (S-DALINAC) is an electron linear accelerator operated by the Institute of Nuclear Physics at the TU Darmstadt. Initially, the accelerator was designed as a twice-recirculating accelerator. In continuous wave operation mode, the specified maximum energy is 130 MeV. Since 2016, the accelerator is a thrice-recirculating electron linear accelerator.
In order to obtain the path components of the accelerator beamline, i.e. the positions and the orientations of the dipole and the quadrupole magnets as well as the position and alignment of the beam tube between the cryostat modules, the TU Darmstadt collaborates with the Laboratory for Industrial Metrology and measurement campaigns were initiated and were performed at S-DALINAC. Based on the results of the measurement campaigns, the electron linear accelerator was enlarged and was equipped by a third recirculation in 2016.
Tasks and challenges
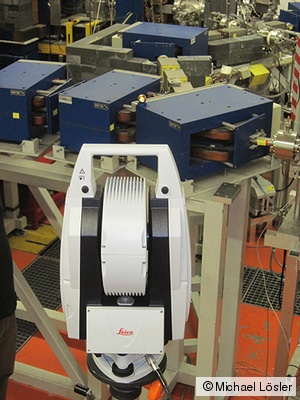
The required accuracy of a spatial position was specified by 0.5 mm. For that reason, the Laboratory for Industrial Metrology used the mobile laser tracker AT401 (Hexagon/Leica). The measurement uncertainty of an observed spatial position is specified by 15 µm + 6 µm/m. Beside the high measurement accuracy, the mobile laser tracker AT401 is characterised by its compact design and allows for flexible and optimal stationing of the instrument at almost any position at the accelerator.
In total, 66 magnets defining the beam line, i.e. 26 dipole magnets and 40 quadrupole magnets, as well as parts of the beam tube between the cryostat modules were observed tactilely. More that 1500 points were measured using about 30 instrument stations and more than 2100 polar observation triples. A polar observation triple is defined as a spatial distance, a direction angle, as well as a zenith angle measurement. The object based reference frame defining the datum of the accelerator was realised by 18 drift nests. To reduce the down time of the accelerator, the measurement campaign was carried out within two weeks. For staking out and aligning path components of the beamline, the Omnitrac 2 (API) laser tracker was used as well.
As a joint project, the electron linear accelerator S-DALINAC was measured by the FARO Focus3D S 120 laser scanner. The registered three-dimensional point cloud is used for simulations or virtual reality. It allows a visualisation and a safe analysis during the regular accelerator process without having access to the hall of the accelerator.
Analysis and adjustment strategies
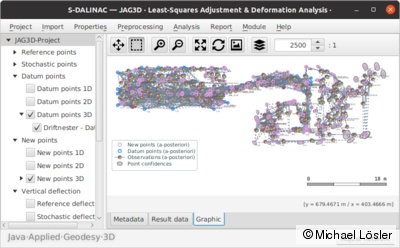
A network adjustment was carried out to combine the conducted observations, which were taken from several instrument stations as well as from different instruments, in a consistent reference frame. For that purpose, a Cartesian coordinate based bundle adjustment software package was developed by the Laboratory for Industrial Metrology. Following the recommendations of the Guide to the Expression of Uncertainty in Measurement (GUM), the in-house software package combines specified so-called Type A and Type B uncertainties having different statistical distributions. Thus, a comprehensive uncertainty budgeting is applied. Errors in linearization are minimised by performing a Monte Carlo simulation or a so-called Unscented Transformation, which is known to involve less computational burden. Since 2016, the in-house software package Java·Applied·Geodesy·3D (JAG3D) is used to perform a rigorous network adjustment on the observation level.
Estimation of a double cylinder
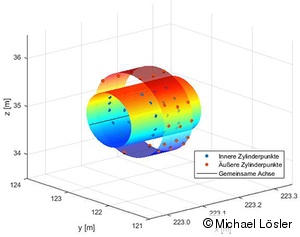
The estimated coordinates of the network adjustment as well as the related dispersion matrix were used to fit parameters of geometric primitives defining the beamline. For instance, the surface of the beam tube between the cryostat modules is cylindrical in shape. Due to the measurement configuration, the resulting surface can be parameterised by a double cylinder. The axis of the double cylinder corresponds to the beamline. The curve and surface analysis was also applied to derive the orientation and the tilt of the beamline components such as dipole and quadrupole magnets. For that purpose, a plane-fitting algorithm is used like for the analysis of the multibeam echosounders. The achieved uncertainty of a spatial position is about 0.2 mm (k=2) and fulfils the accuracy requirements.
Eschelbach, C., Lösler, M., Steinhilber, G., Birkhan, J., Arnold, M., Pietralla, N.: Indirekte Bestimmung des Pivot-Punktes eines Magnetspektrometers mittels mobiler Lasermesstechnik. In: Wieser, A. (ed.): Ingenieurvermessung 23: Beiträge zum 20. Internationalen Ingenieurvermessungskurs, Zurich, 11-14 April 2023, Wichmann, pp. 418-431, 2023. ISBN: 978-3-87907-734-2
Arnold, M., Burandt, C., Grewe, R., Pforr, J., Pietralla, N., Steinhorst, M., Eschelbach, C., Lösler, M., Hug, F.: First ERL Operation of S-DALINAC and Commissioning of a Path Length Adjustment System. In: Koscielniak, S., Satogata, T., Schaa, V., Thomson, J. (eds.): Proceedings of 9th International Particle Accelerator Conference (IPAC2018), 29 April-4 May 2018, Vancouver, Canada, pp. 4859-4862, 2018. DOI: 10.18429/JACoW-IPAC2018-THPML087
Arnold, M., Burandt, C., Eschelbach, C., Kürzeder, T., Lösler, M., Pforr, J., Pietralla, N.: ERL Mode of S-DALINAC - Design and Status. In: Proceedings of ERL17 - The 59th ICFA Advanced Beam Dynamics Workshop on Energy Recovery Linacs, 18-23 June 2017, CERN, Geneva, Switzerland, 2017. DOI: 10.18429/JACoW-ERL2017-MOIDCC006
Arnold, A., Burandt, C., Eschelbach, C., Lösler, M., Pforr, J., Pietralla, N.: The Thrice-Recirculating S-DALINAC with ERL-Mode. In: Aulenbacher, K., Khoukaz, A. (eds.): 650th WE-Heraeus Seminar, Physics of Energy-Recovering Linacs, 16-18 October 2017, Bad Honnef, Germany, 2017.
Eschelbach, C., Lösler, M., Winkemann, P., Arnold, M., Pietralla, N.: Einsatz mobiler Lasermesstechnik bei der Erfassung von Strahlführungselementen eines Elektronenlinearbeschleunigers. avn - Zeitschrift für alle Bereiche der Geodäsie und Geoinformation, 124(3), pp. 61-69, 2017.
Eschelbach, C., Lösler, M., Winkemann, P., Arnold, M., Pietralla, N.: Einsatz mobiler Lasermesstechnik zur Aufnahme von Strahlführungselementen eines Elektronenlinearbeschleunigers. In: Luhmann, T., Schumacher, C. (eds.): Photogrammetrie - Laserscanning - Optische 3D-Messtechnik: Beiträge der 15. Oldenburger 3D-Tage 2016, Wichmann, pp. 307-318, 2016, ISBN: 978-3-87907-604-8
Lösler, M., Arnold, M., Bähr, H., Eschelbach, C., Bahlo, T., Grewe, R., Hug, F., Jürgensen, L., Winkemann, P., Pietralla, N.: Hochpräzise Erfassung von Strahlführungselementen des Elektronenlinearbeschleunigers S-DALINAC. Zeitschrift für Geodäsie, Geoinformatik und Landmanagement (ZfV), 140(6), pp. 346-356, 2015, DOI: 10.12902/zfv-0090-2015
Prof. Dr.-Ing.
Cornelia Eschelbach
Phone: +49 (0) 69 1533-2356
cornelia.eschelbach(at)fra-uas. de
Dr.-Ing.
Michael Lösler
Phone: +49 (0) 69 1533-2784
michael.loesler(at)fra-uas. de
Address
Transfer centre
Steinbeis Transfer Centre Applied Geodesy
https://applied-geodesy.org
Member of SCGD
Member of the Society for Calibration of Geodetic Devices e.V. (SCGD)